Why Reliable Production Tool Supply Chains Matter More Than Ever
- CTIS
- Mar 4
- 4 min read
Updated: Apr 23
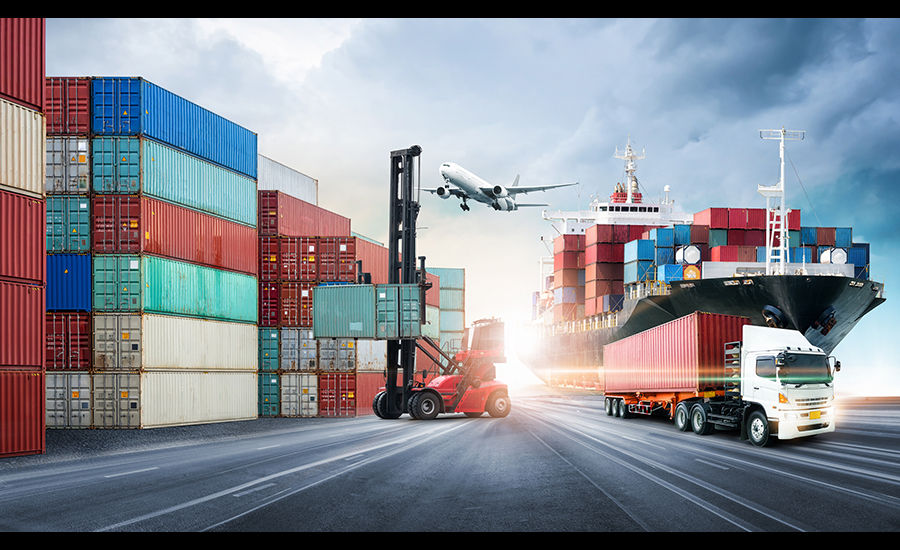
A reliable supply chain is the backbone of any successful manufacturing operation. In today's fast-paced and increasingly unpredictable global market, securing a consistent and high-quality source of production tools is more critical than ever. Disruptions in the supply chain can lead to downtime, increased costs, and lost business opportunities.
Whether you operate a small machine shop or a large-scale industrial facility, having access to the right tools at the right time is essential for maintaining productivity, meeting deadlines, and staying competitive. This article explores why supply chain reliability matters and how manufacturers can safeguard their operations.
The Growing Challenges in Production Tool Supply Chains
Supply chain disruptions have become a major concern for manufacturers worldwide. From raw material shortages to shipping delays and geopolitical instability, various factors have made it increasingly difficult to source production tools efficiently.
Some of the biggest challenges impacting production tool supply chains today include:
Rising costs of raw materials and components: Geopolitical uncertainties and global events have led to significant instability in the cost of energy and raw materials, affecting manufacturing inputs.
Increased shipping delays due to port congestion and transportation shortages: Recent conflicts and industrial strikes have added to these challenges, extending transit times, especially from Asia to Europe and the US.
Global events such as pandemics, trade disputes, and natural disasters affecting supply routes: The COVID-19 pandemic and geopolitical tensions have led many companies to diversify their supply chains to mitigate risks.
Limited availability of skilled labor in manufacturing and logistics: Labor market tightness continues to impact manufacturing and supply chain operations.
Cybersecurity threats disrupting digital supply chain operations: As supply chains become more digitized, they face increased exposure to cyber threats, necessitating robust cybersecurity measures.
A survey by Deloitte revealed that 72% of manufacturing executives believe that persistent shortages of critical materials and ongoing supply chain disruptions present the biggest uncertainty for the industry in the coming year.
The Cost of an Unreliable Tool Supply Chain
When manufacturers do not have access to the tools they need, production slows down, deadlines are missed, and costs rise. Some of the most significant consequences of an unreliable tool supply chain include:
Unplanned downtime due to missing or delayed tools: Supply chain delays continue to impede the timely receipt of key components, affecting manufacturing products.
Increased maintenance and repair costs from using outdated or subpar equipment: Reliance on outdated tools can lead to frequent breakdowns, escalating maintenance expenses.
Higher lead times for product completion, leading to dissatisfied customers: Supply chain disruptions have significantly increased transportation costs and container prices, resulting in higher costs for businesses and extended delivery times.
Loss of revenue and potential contracts due to operational inefficiencies: Operational disruptions can erode customer trust and result in lost business opportunities.
According to a Deloitte study, 80% of surveyed manufacturing executives have experienced a "heavy" to "very heavy" impact of disruption on their supply chains over the past 12 to 18 months.
How a Reliable Supply Chain Improves Manufacturing Efficiency
A well-structured and dependable supply chain ensures that production tools are readily available when needed, reducing delays and improving operational efficiency. Key benefits include:
Consistent availability of high-quality tools and equipment: Ensures that manufacturing processes run smoothly without interruptions.
Reduced risk of production stoppages and downtime: A reliable supply chain minimizes the chances of unexpected halts in production.
Improved cost predictability and better financial planning: Stable supply chains allow for more accurate budgeting and forecasting.
Enhanced supplier relationships leading to priority service and support: Strong partnerships with suppliers can result in better service levels and responsiveness.
Greater flexibility to respond to market changes and customer demands: A resilient supply chain enables manufacturers to adapt swiftly to changing market conditions.
Manufacturers that invest in supply chain resilience see a significant reduction in costs associated with emergency procurement and last-minute supplier changes. By working with trusted partners like CTIS, businesses can secure a stable supply of essential production tools.
Strategies for Strengthening Your Tool Supply Chain
Building a more reliable supply chain requires proactive planning and strong supplier relationships. Here are some strategies manufacturers can implement to improve supply chain resilience:
Diversify Supplier Networks
Relying on a single supplier increases the risk of delays and shortages. Manufacturers should work with multiple suppliers across different regions to mitigate the impact of disruptions.
Implement Inventory Management Systems
Using advanced inventory tracking and forecasting tools can help businesses anticipate demand fluctuations and prevent shortages. Predictive analytics can also help optimize stock levels without over-purchasing.
Strengthen Supplier Relationships
Long-term partnerships with reliable suppliers can ensure priority service, better pricing, and faster response times during supply chain disruptions. Manufacturers should regularly communicate with suppliers to stay ahead of potential issues.
Invest in Local Sourcing
While global suppliers offer competitive pricing, local sourcing can provide a safety net during international trade disruptions. Having a mix of local and international suppliers ensures flexibility.
Utilize Digital Supply Chain Solutions
Many manufacturers are now leveraging artificial intelligence and blockchain technology to improve supply chain transparency. Digital tracking systems help monitor shipments in real time, providing better control over sourcing and delivery.

Conclusion
A reliable production tool supply chain is no longer just a competitive advantage; it is a necessity for manufacturers navigating today’s unpredictable market conditions. Companies that prioritize supply chain resilience benefit from reduced downtime, improved cost efficiency, and the ability to meet customer demands consistently.
Partnering with a trusted supplier like CTIS ensures manufacturers have access to high-quality tools, dependable delivery schedules, and expert support. Contact CTIS today to learn how a stronger supply chain can improve your manufacturing
Comments